Health and Safety Culture in the Workplace
We’re passionate about workplace safety.
Just ask anyone who works at a Maple Leaf Foods site. We’re committed to being a global leader in workplace safety.
Promoting a good health and safety culture
Our Occupational Health and Safety (OHS) goal is clear and ambitious: zero occupational injuries. We promote a workplace safety culture that encourages people to follow safety protocols, to use safety equipment, to identify hazards, and to speak up when they have any concerns.
Our safety record is industry-leading. We had zero fatalities in 2024, a trend we’ve sustained for more than a decade. Even so, we’re constantly looking for ways to make our workplaces even safer.
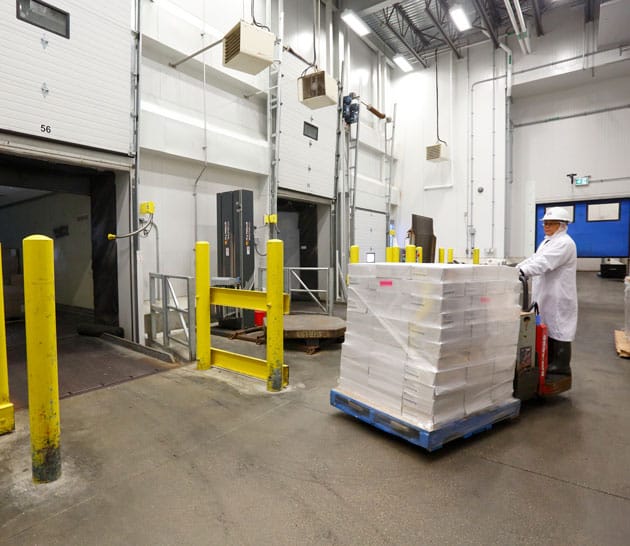
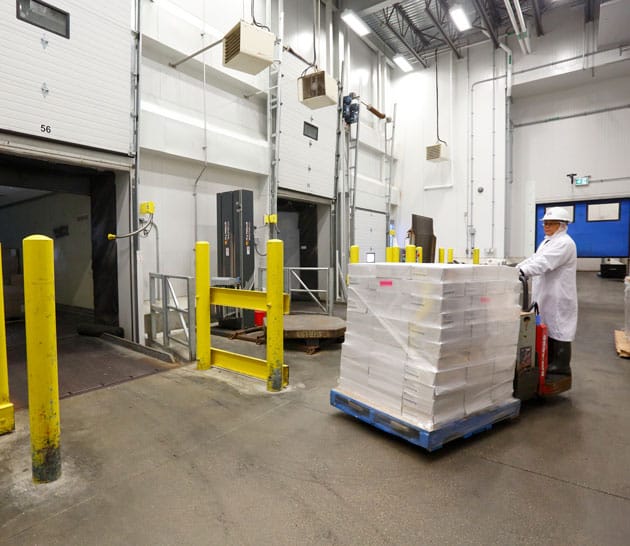
*TRIR represents the number of recordable incidents per 100 full-time workers for a given period. The definition of a recordable incident is in accordance with the Occupational Safety and Health Administration (OSHA) standard and the total hours worked for salary and hourly team members are based on internal payroll data. This is applicable to all Maple Leaf Foods sites, including new or acquisition plants’ baseline year results beyond their one-year transition to implement and integrate into our OHS management system. This performance indicator is within the scope of KPMG’s limited assurance report (see ‘External Assurance’ for details).
**These sites also include groupings of our owned/leased hog barns in addition to our plants and offices in Canada, United States, and Asia.
Our Total Recordable Incident Rate (TRIR) improved by 93.6% in 2024 when compared to our 2012 baseline reporting year.
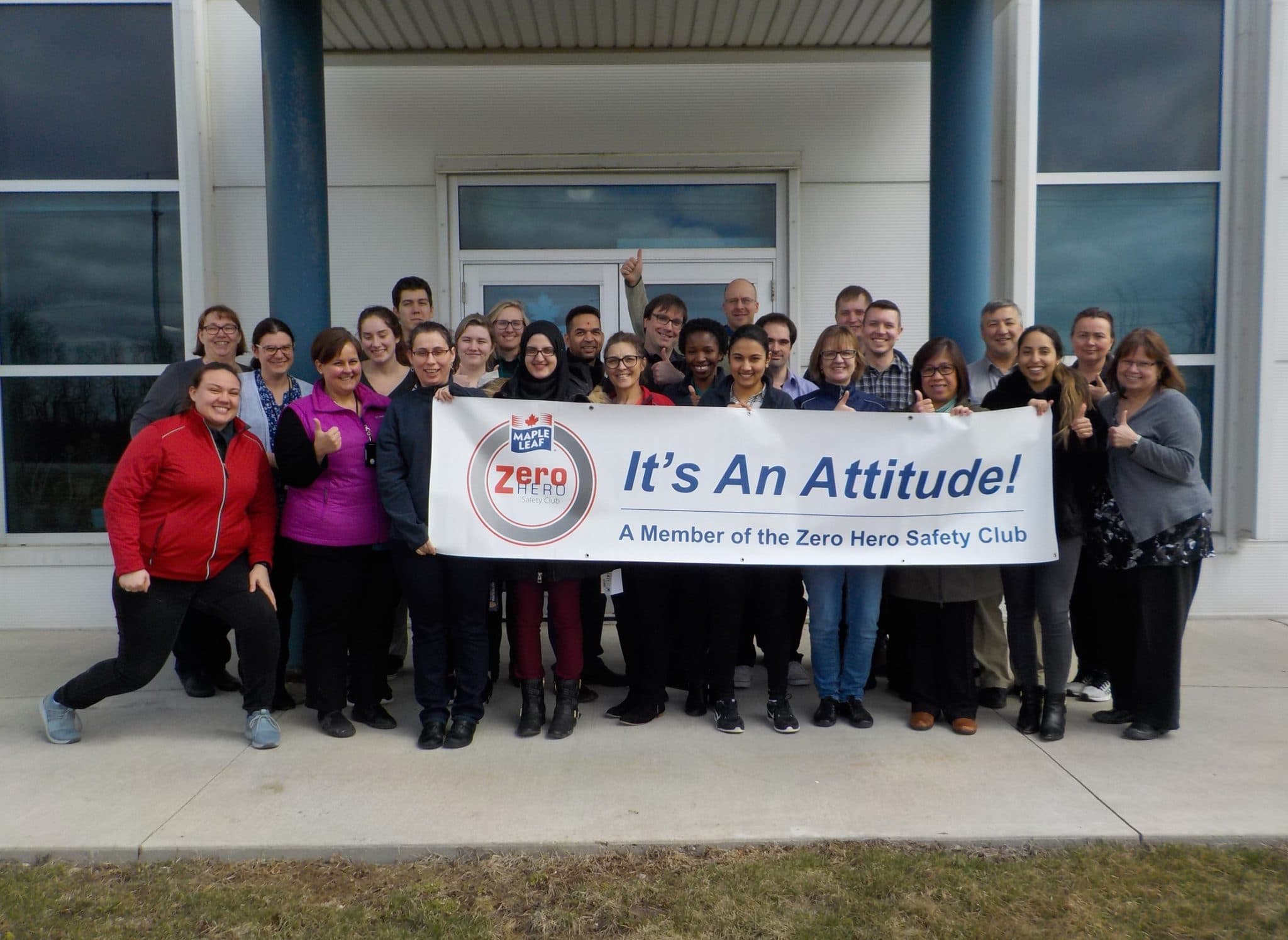
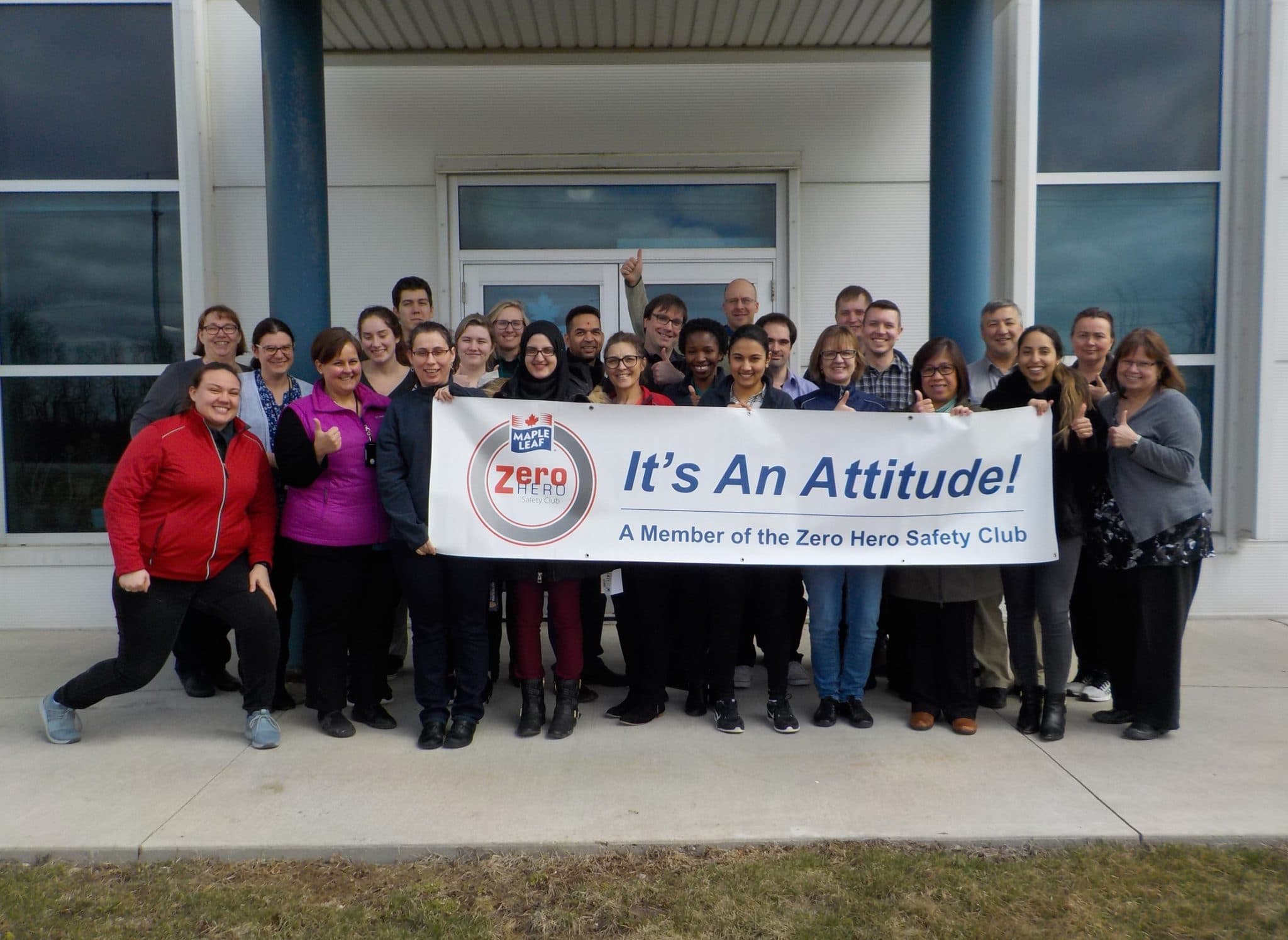
Occupational Health and Safety in the workplace is very important to us
We don’t want our people getting hurt on the job. Not on our watch. We’ve created an internal program, the “Zero Hero Safety Club”, so our Team Members can be our partners in achieving our goal of zero occupational injuries. Our sites become members of the Club when they achieve zero occupational injuries, along with other criteria.
In 2024, 33 sites* had zero recordable injuries, and of those, 20 sites we’re proud members of the Zero Hero Safety Club!
*These sites also include groupings of our owned/leased hog barns in addition to our plants and offices in Canada, United States, and Asia.
Occupational Health and Safety management
We have an Occupational Health and Safety (OHS) management system across all Maple Leaf Foods sites based on our OHS policy, programs, and various other standards that we have adopted to create the safest possible work environment. We created this OHS management system to ensure that we comply with and even exceed Occupational Health and Safety regulations.
Each Maple Leaf Foods site has a Joint OHS Committee that represents all our Team Members. These formal joint management–employee committees monitor and advise on OHS programs, identify potential hazards and recommend controls. The Joint OHS Committees ensure that our plants comply with all federal and provincial health and safety regulations. All of Maple Leaf Foods’ sites (57 sites plus three new sites in 2020) have a Joint Health and Safety Committee that is represented by management and employees.
We want all of our sites to own their program management, to help improve the system, and to develop future safety action plans.
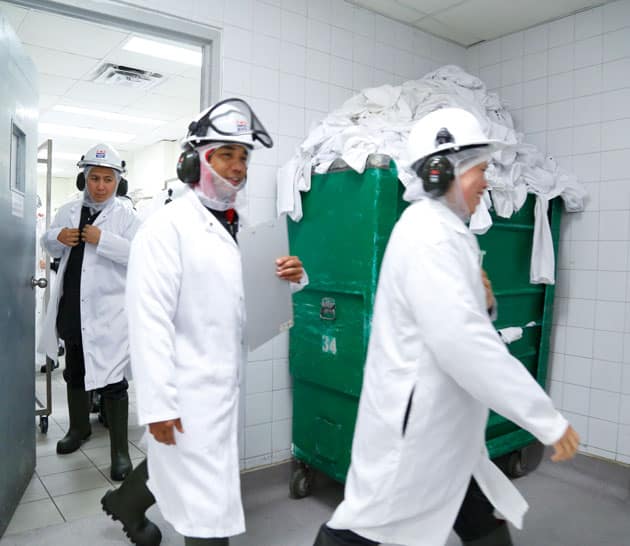
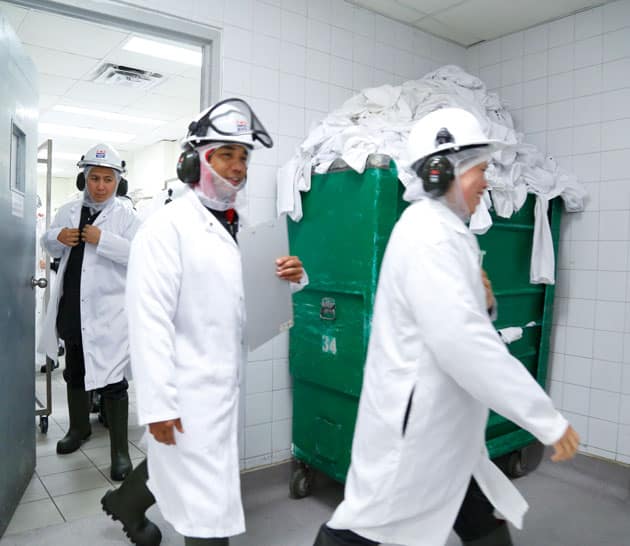
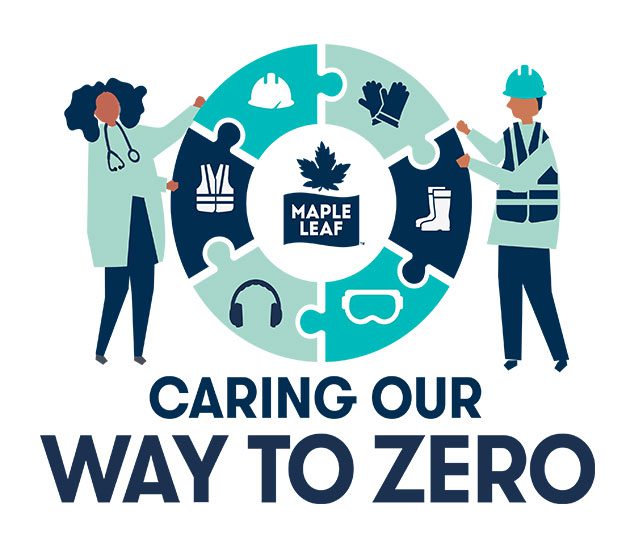
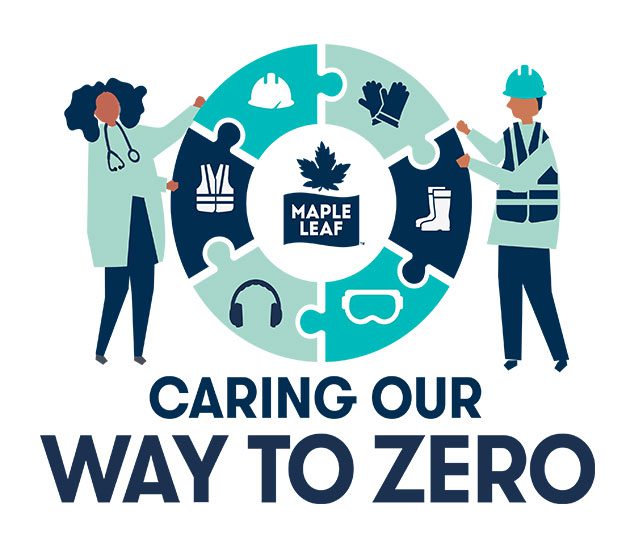
Caring our Way to Zero
Maple Leaf Foods unveiled a new OHS framework centred around “Caring our Way to Zero” to reaffirm our ongoing commitment to our Team Members that their safety, health, and well-being are our number one priority.
Our new “Caring our Way to Zero” framework is comprised of four elements: standardization, governance, recognition, and validation. Each of the elements include initiatives and tools that activate on the framework and promote awareness and educate Team Members about the importance of working together to implement healthy practices.


Identifying work-related hazards
Our workers, supervisors, and managers conduct monthly inspections to identify any work-related hazards. Our preventative maintenance programs, hazard reporting programs, and job safety analyses are among the processes that we put in place to help identify hazards before they cause an injury.
We have an incident investigation standard that all of our sites must adhere to. All incidents must be reported immediately and investigated within 24 hours.
We provide training on incident investigation, hazard identification, risk assessment and other Maple Leaf Foods standards and standard operating procedures. We want our people to have the tools and knowledge to identify work-related hazards and to prevent injury.
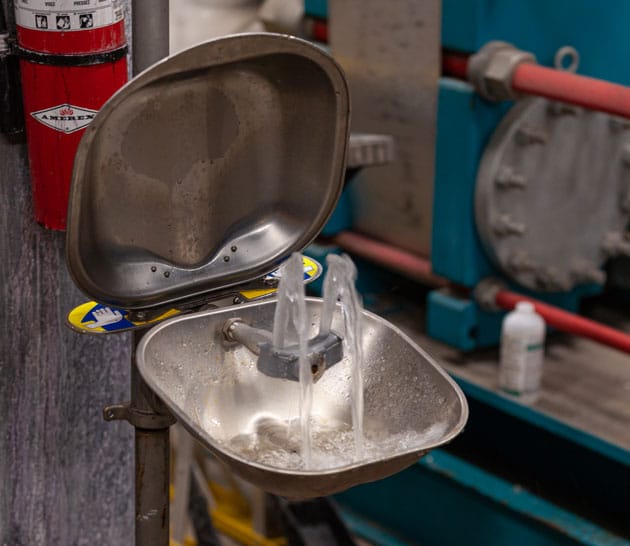
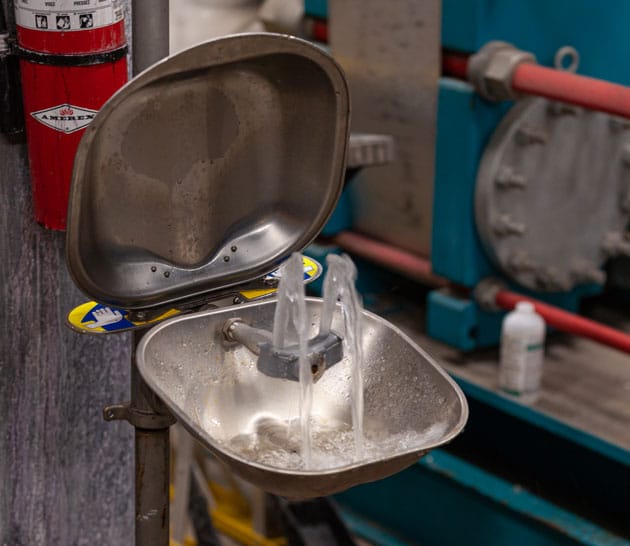
Occupational Health and Safety training and communication
Training our people on Occupational Health and Safety (OHS) is crucial to ensuring they understand the risks and hazards that could occur on the job and how to handle them.
All new Team Members receive a comprehensive OHS orientation covering Maple Leaf Foods’ safety standards, the site’s standard operating procedures, safety rules, safe work procedures, and emergency response procedures.
Ongoing skills development and training are essential to reinforce the importance of OHS and to continually strengthen our safety culture.
Integrated Report
We’re documenting all the changes we’re making. See our progress in our latest Integrated Report.