How our organization raised the bar on worker safety and created industry-leading safety performance.
By Mike Walsh, VP, Health, Safety, Security, and Environment
At Maple Leaf Foods, we’re passionate about making good food. And we’re passionate about our people too. This fall marks 10 years since Maple Leaf Foods created its Occupational Health and Safety Strategy and set a bold new goal of less than a total recordable incident rate (TRIR) of 0.9 by 2016. That goal was achieved, and a bolder goal was set for a TRIR of 0.25 or less by 2026. That ambitious commitment to our people set in motion a decade of progress in protecting our people and achieving industry-leading results. At the ten-year mark, it’s time to reflect on how we’ve achieved our safety progress — and will continue to advance towards our goal.
Recognizing our problem — and attacking it
When I joined Maple Leaf in 2012, our CEO, Michael McCain, asked for a formal Occupational Health and Safety (OHS) Strategy to support the Safety Promise for a path to industry leading safety levels.
Our assessment revealed that too many recordable injuries occurred at our sites in 2012 and this was unacceptable. (Recordable injuries are those serious enough to require medical treatment or lost time from work.) But our CEO didn’t just want a 10% reduction in the TRIR; he wanted a path to ZERO. Getting from a TRIR of 6.25 in 2012 to zero was a big ask and I knew it would take a big culture change and a whole lot of teamwork to achieve our new goal.
It’s easy to fall into the habit of striving to be average in performance and believing that injuries are just inevitable given the nature of our work. We decided we would reject this outdated view of inevitability and focus on the possibility of an injury-free workplace. To help our teams understand what was possible, we set incremental goals and sought to achieve them over time.
Radical internal transparency and partnership with all stakeholders
We decided that radical internal transparency and partnership with site leaders and designates were an important first step. We had best-in-class leaders who needed help with building annual plans to drive the OHS results. Our Senior OHS Team began communicating our injury rates by site every month throughout our company. It was beyond the Excel spreadsheet reporting. That new OHS report became one of best motivators we ever created because every site wanted to lead — no site wanted to be ranked last in safety performance. Healthy competition resulted, and we began to see increased focus and sustained progress.
We also launched quarterly Safety Promise meetings with our CEO, senior leaders, and site managers to increase the focus on safety performance. Today, our CEO engages directly with site leaders any time a significant or critical safety incident occurs, and our vice presidents follow up with sites about ANY recordable injury. We look for the root cause and how we can prevent the incident from recurring.
Working with our site OHS designates and leaders, we were striving towards the next step in our safety journey.
Today, we also share the facts around any recordable injury throughout the company to ensure accountability and to help others learn from the incident so they may prevent anything similar from occurring at their sites.
Celebrating progress
Just as we embraced radical transparency in showcasing performance that is good and performance that has improvement opportunities, we also recognized the need to celebrate outstanding performance. We started by creating an Annual Safety Awards Ceremony that recognizes great performance. We then launched a “Zero Hero Safety Club” that awards the “Zero Hero” title to any large site without a recordable injury for the prior six months, and to any small site without a recordable injury for the prior 12 months, as well as other criteria.
Membership in this “club” is coveted and can be lost with a single recordable injury. When we launched the Club in 2016, there were only two sites that were Zero Hero Safety Club members. By the end of 2022, there were 19 Zero Hero Safety Club members.
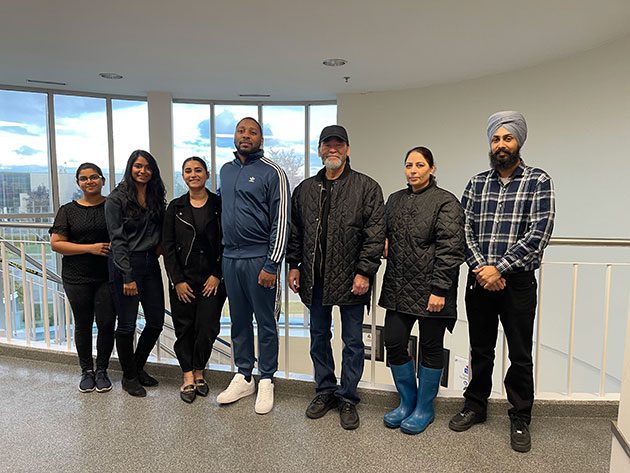
Equipment and systems
As our safety culture flourishes, we recognized that unsafe equipment dictates unsafe behaviour. As a result, we invested in better, more effective safety gear to protect our Team Members. This includes guarding, mobile equipment, and personal protective equipment.
At the same time, we implemented systems and practices proven to ensure that equipment was used properly and that all our practices advanced us toward our safety goals. For example, we partnered teams to establish effective lockout/tag out programs to prevent injuries.
The proof is in the data
The success of any safety program is defined by the results and workers going home safely every day to their families. And the data shows that our approach has worked.
In 2016, Maple Leaf site teams were moving from “good to great.” Michael McCain’s challenge to reach a “bold” target of having less than one Total Recordable Injury Rate (TRIR) by 2016 was achieved. In fact, Maple Leaf Foods’ 2016 TRIR was 0.78 with 14 out of the overall 52 sites achieving a TRIR of 0.00.
By 2022, we had reduced our recordable incident rate by 92.3% over the 2012 year-end results. We had also reduced the number of incident reports by 91.9% — from a TRIR of 6.25 in 2012 to 0.48 recordable incidents in 2021.
What do those numbers mean in the big picture? Our safety program is in the top quartile in the North American Bureau of Labor Statistics for all manufacturing!
Still, we recognize that patting ourselves on the back for too long won’t help our safety programs. And so, with our aspirational goal of zero injuries still on our minds, early in 2022, we set a “greater bold goal” for our company: to achieve a TRIR of 0.25 or less by 2026, while still holding our aspirational goal to achieve zero injuries in the workplace.
The bold new goal means we must provide the right training and ‘how to’ guide to foster safe working environments. It also means measuring how we’re doing and tracking the results, as well as celebrating our successes when they come along.
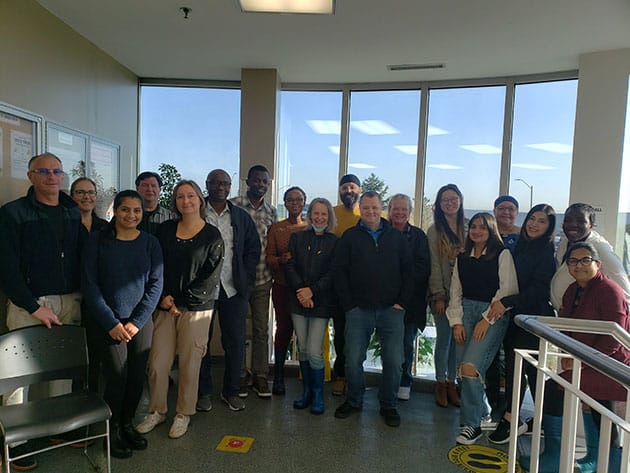
Putting our safety culture to the test
As our confidence in our safety programs and culture grew, we were stunned to be tested by an invisible enemy: COVID-19. And it was in 2020 when we realized how well our safety culture and our disciplined approach would serve us during a global pandemic in ensuring occupational health and safety.
Partnership with sites and a safe culture were the foundation. Credit goes to many Team Members and our sites.
When the pandemic was declared in March 2020, we quickly rolled out the pandemic playbook we had developed. We deployed a variety of new practices, including daily health screenings, masking, physical distancing within our operations, scrupulous sanitation, and a “stay home when sick” culture. Although COVID-19 touched each of our operations, we were acknowledged by public health officials and similar industries that we were leading the way with managing COVID-19. A safe culture at our sites enabled us to deliver a best practice pandemic plan. A shout-out to all the Team Members, leaders, and every one of us who played a significant part of ensuring the safety of our workers!
When vaccines became available, we also took a bold stand in support of them. We hosted vaccine clinics at our operations and offered paid time off for Team Members to go to community clinics. We ultimately adopted a policy requiring ALL Team Members to be fully vaccinated because we believe it’s the best way to protect our people and our communities.
Helping our Team Members feel safe
Beyond the progress our data reflects, there’s more data that’s incredibly gratifying. Our annual Team Member engagement surveys show that our Team Members feel that our safety culture is one of our greatest strengths. They FEEL safe when they come to Maple Leaf sites because they ARE safe.
I asked our Chief Food Safety and Sustainability Officer, Randy Huffman, for his reflection at the 10-year mark. “I’m so proud, first and foremost, of the central team for establishing standards and executing a standardized approach across the network,” he says. “I’m just as proud of all the people in the facilities, plants, and our farm operations who bought into that standardized approach and executed it every day.”
Brent Holmes, Plant Manager at the Courtneypark plant in Mississauga, Ontario, says his experience in several Maple Leaf facilities since the strategy was rolled out has been inspiring. “I can say without a doubt that it’s had an enormous impact on safety culture and accident reduction. My sites have all experienced year-over-year improvements with very few setbacks. Team Members working on the floor are more engaged, they’re able to identify risk, and they’re willing to act on risk and communicate.”
Brent adds that our OHS Strategy proved intimidating at first: “In the beginning, everyone was taken aback by the target of zero injuries, but all agreed that it’s the right target to strive for. Why target anything less?”
Kimberly Palmer, Health & Safety Manager at our Lagimodiere, Manitoba plant, offered the ultimate compliment when she told me she’s proud to have her own son work at Maple Leaf over the summer. “I’ve always promoted that it must be safe enough for my family to work here. I had no concerns bringing him on because I know that we have a great safety culture and strong programs in place.”
Ten years after we rolled out our program, what does the man who posed the challenge have to say? According to our CEO, Michael McCain, “Our mission is clear: no one gets hurt at Maple Leaf Foods. In 2022 so far, 31 sites achieved this — and it is within our grasp to ensure that all sites reach zero recordable incidents in the future.”
And with that challenge from Michael, it’s time to get back to work and stay focused on building our safe work culture and reaching our ultimate goal: ZERO occupational injuries.
Over the past ten years, as VP, Health, Safety, Security, and Environment, it’s been an honour to work with a great group of leaders and Team Members who have come together to work collaboratively to ensure our workers go home safely every day to their families!